
Dry Dock of Main Fleet & Offshore Vessel
A dry dock is a controlled space used for building, fixing, and maintaining boats and commercial ships. This special design or setup makes it possible for water to fill up a space, sometimes referred to as a lock, allowing boats to maneuver into and out of the region.
​
The gates are shut once the ship enters the dry dock, and the water is drained out to expose the hull and other sections of the ship that have been exposed to the sea for an extended period of time to maintenance and repair work.
​
Survey of Dry Docks
​
All merchant vessels must undergo an intermediate survey within 36 months of the first full survey in a dry dock, and a thorough survey of the hull twice within five years, according to SOLAS regulations.
This covers upkeep on the ship's hull, propeller, rudder, and other submerged components that are typically out of reach for crew members when sailing.
Every year, a passenger vessel's bottom needs to be inspected. It is necessary to conduct two of these examinations in dry dock over a five-year period, with a maximum three-year gap between them.
​
Different Dry Dock Types
A variety of dry dock types are employed in ship maintenance and repair. Primarily, they are: 0.50
​
-
Graving Dry Dock
-
Floating Dry Dock
-
Marine Rail Dry Dock
-
Shiplifts Dry Dock
-
Marine Mobile Lifts Dry Dock
​
The marine mobile lifts and ship lifts are the most commonly utilized among them for small vessels, including pilot boats, tugboats, and leisure yachts.
Currently, seagoing vessels use two primary types of dry dock processes from the above list:
​
1) Graving Dry Dock
​
Usually, this kind of dry dock is built on land close to coastal seas. It has walls, gates, and blocks. It is rectangular and constructed of solid concrete. After being moved inside the dry dock, the ship is placed on the blocks. The water is evacuated and the gate is closed after the ship is in the proper place.
​
Historically, stones and wood were used to build the graving dry docks. The pier is now sealed with a hefty steel gate to prevent water intrusion while the ship is standing on the blocks. The enclosure is made of steel and concrete.
​
The gates can be one solid steel structure supported on a roller over the track that can be retracted inside the dry dock walls when opening the gate, or they can be two pieces that are individually hydraulically controlled and hinged to the sides.
​
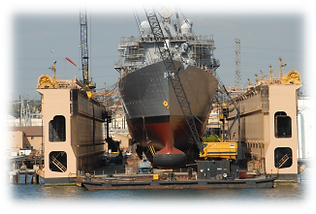

Benefits of Graving Dry Dock
-
Compared to other dry docking systems, it can handle larger vessels.
-
Comparing a vessel of the same size to other types, dry docking is less expensive.
-
Unlike other varieties, the graving dry dock may execute modifications, retrofitting, and other tasks.
-
The graving dock's proximity to the land makes it simple to get supplies of machinery, spare parts, and services.
-
Modern sophisticated graving docks feature elevated surfaces for hot work, welding, and other workshops, providing easy access and efficient workflow within the dock—above the water's surface when the dock is full.
-
New graving docks with retractable ramps make it simple to deliver spare parts and reduce labor and time required to move them inside the port.
-
More than two ships can be repaired simultaneously on a larger graving dock, and some contemporary graving docks feature two gates at either end, which facilitates independent vessel repair and refloating.
​The drawbacks of using Graving Dry Dock
-
​​Re-flooding the dry dock requires removing all of the apparatus and equipment from the dock, which is a time-consuming process.
-
As the graving dock ages, its maintenance costs rise and eventually reach extremely high levels.
-
If there is an issue with the dock gate, the entire dock will become inoperable.
-
Compared to other methods of docking, the graving dock requires more time for the docking and undocking operation.
-
If the dock is used to repair numerous ships, all operations must stop if one of the ships needs to be removed from the dry dock because it will need water to be filled in order to float again.
The floating dock is de-ballasted once the ship is in position in order to remove the water from its hollow walls and flooring, which support the ship on the blocks placed on the dock's floor.
There is a valve that may be opened to submerge the dock and fill the chambers with water, allowing the ship to set sail.When the chamber's water is drained out, the dry dock rises and the ship's submerged section is visible for maintenance or repairs.Typically, ballast tanks are installed on the sides and bottom of the floating dry dock to enable dock raising and lowering.
The steel structure of the dock is akin to that of seagoing boats.Floating dry docks are frequently used in protected harbors devoid of tidal activity or waves.

The floating dock is de-ballasted once the ship is in position in order to remove the water from its hollow walls and flooring, which support the ship on the blocks placed on the dock's floor.
There is a valve that may be opened to submerge the dock and fill the chambers with water, allowing the ship to set sail.When the chamber's water is drained out, the dry dock rises and the ship's submerged section is visible for maintenance or repairs.Typically, ballast tanks are installed on the sides and bottom of the floating dry dock to enable dock raising and lowering.
The steel structure of the dock is akin to that of seagoing boats.Floating dry docks are frequently used in protected harbors devoid of tidal activity or waves.
Benefits of Dry Docking on the Water
-
They can be driven to a salvage vessel located close to the harbor
-
.They have a higher resalable return and require less maintenance than graving docks.
-
Because they may be positioned inside the harbor close to or far from the coast, they are a movable and space-saving building that doesn't take up any room on the shore facilities.
-
By ballasting the dock, the entire floating dry dock can be trimmed forward or aft, further assisting the ship or the damaged vessel that cannot be trimmed.
-
To stabilize the floating dry dock, more mooring gear is required
-
The floating dry dock can be extensively retrofitted or rebuilt to enhance its size in all dimensions.
-
They can also be divided into two distinct floating docks that are separate from one another.
​
Negative aspects of floating dock
-
One entry point, or gangway, is typically used for the supply of stores, equipment, and labor, which slows down operations.
-
Because the hull of a floating dry dock is submerged in saltwater, maintenance costs are comparable to those of a ship.
-
The operation of the floating dry dock will be impacted by windy or tidal conditions.
-
It takes time to remove all the necessary apparatus and equipment before flooding the dock again.
​
Sections of Dry Dock
The ship's burden is divided among the blocks situated beneath the keel plates in large part thanks to the blocks inside the dry dock. Each ship comes with a docking document that offers a ship classification society-approved guide block plan.
The blocking plan for the specific vessel, as well as how the ship will operate when resting on the blocks while under load—including the several factors that can influence the load a block takes—must be understood by the shipmaster/chief officer and the dry dock master.
To ensure that the blocks are all around the same rigidity, they are often made of a single material. The force applied to the blocks with a smaller elasticity module will squeeze them more than the stiffer block if the blocks are made of different materials. This may cause the block or the ship's hull to sustain damage due to the uneven distribution of force.
​
The most often utilized materials for the blocks are:
-
Timber blocks
-
Concrete with steel
-
Concrete at the bottom and timber at the top
-
A timber block will support substantially less weight than the other blocks when placed to a keel track composed of blocks with steel or concrete bases.
-
Side blocks are also set to support the ship in addition to the keel blocks. They are not as stiff as the keel blocks because a stiffer side block may overburden the boat and cause structural damage. Generally speaking, the slide blocks' height is equal to or greater than the keel blocks'.
-
The following are significant variables that impact the loading on the dry docking blocks:
-
The block's initial height is a crucial component to consider, as the load shared by all the other blocks will determine the load on each individual block. The load distribution will be even if the blocks are positioned and raised in accordance with the ship's hull.
-
The load distribution on the block is determined by the contact area of the block with the ship's hull. If the block's contact area is smaller than its size, then less load will be applied to it than on a block with a bigger contact area.
-
The block's material: As previously mentioned, various materials have distinct reactions to the force applied by the vessel. Therefore, the ship's alignment in the dry dock is significantly influenced by the material of the side and keel blocks.
-
Block placement: The ship's docking plan must be followed when placing the blocks in the dry dock. If the block location is left unchanged, numerous kinds of machinery and components may sustain harm. Echo sounders, anodes, and other equipment tools require space to settle once the ship lands on them, thus the blocks containing them must be removed.
​
Selecting a Dry Dock Type
The following variables determine what kind of dry dock is best for a ship:
-
The dimensions of the ship: More sizes can be accommodated with the graving dock than with any other type. The shipowner or manager will use the graving dock if they need to dry dock a big oil tanker. If the vessel weighs around ten thousand tonnes, the marine railway type can be used. A movable marine lift can be used to repair a boat or small yacht in the dock that weighs up to 250 tons.4
-
The state of the ship: Floating docks are frequently utilized when a ship's propulsion plant malfunctions or sustains damage that renders it immobile.
-
Types of repairs: The type of dry dock that is used also relies on the kind of repairs that the ship is seeking. While a floating dock can be chosen for the regularly scheduled dry dock, a graving dock is preferred if significant retrofitting or massive parts/machine fitting is needed. This is because graving docks are typically found close to the shipyard and are easier to move materials from land to dock than floating docks.
-
The location and kind of the dry dock will be determined by the vessel's current timetable and the ease with which the ship can reach the dock after discharging all of its cargo at the final port of call.
-
Budget: The ship's allocated budget is the most important consideration when choosing the type of dry dock.
​
​Requirements for Dry Docking The most crucial prerequisite for successfully bringing a ship into a dry dock is stability.
The following three crucial factors need to be met before entering the dry dock:
-
Sufficient Initial GM: Upon contact with the blocks, the ship has a reaction that elevates its center of gravity (G) and lowers its metacentric height (G.M.). Consequently, a sufficient initial metacentric height is needed to offset this effect.
-
Ship Must Enter Dock Upright: The ship must enter the dock upright, which means there shouldn't be a list to port or starboard when it hits the blocks. A ship may topple over if the point of contact between the keel blocks and the ship is outside the vessel's center line.
-
Small or Moderate Trim Aft: A moderate trim aft is typically maintained when bringing the ship's keel up onto the keel block. The modest trim permits the bow and stern to rise together rather than simultaneously when the dock's water level drops, which lessens the strain and weight on the hull and keel of a ship.​
​
Procedure for Dry Docking
The ship must then be ready to enter the dry dock and its keel must be carefully placed on the blocks that are provided on the dry dock floor once the ship manager has chosen the type of dry dock. A few things to keep in mind are:
-
Make sure the ship is ready to enter the dry dock by removing all cargo and using the least amount of ballast possible.
-
The vessel's state and the docking master's criteria will determine how the ship moves if the floating dock is utilized. The floating dock will approach the ship in the event of an accident immobilizing it, and if the ship is operating well, it may even propel inside the dock.
-
The ship is anchored to the pier once it enters the dry dock.
-
The ship's crew will be informed in advance about the trim need by the docking master.
-
The ship and dock master must make sure that equipment such as an echo-sounder or log sensor is free of obstructions and does not strike any impediments before emptying the dock. Divers are dispatched to verify that all of this equipment is accurate with respect to the blocks.
-
The ship will progressively sit on the keel blocks as the dock master gives the command to pump the water out of the dock.
-
The docking master and the ship’s crew must ensure the point of contact of the ship and keel blocks does not lie outside the centre line of a vessel as it may lead to the tumbling of the ship
-
Once the ship sits on the dock, the cleaning and repairing process starts​
​​
Ship Crew Members' Responsibilities During Dry Docking
The crew of the ship will have the following responsibilities when dry-docking, working under the direction of the chief engineer and chief officer:
-
Maintaining the ship in minimum ballast conditionï‚·Maintaining the aft trim in accordance with the dockmaster's instructions
-
To help the dock crew ensure that the ship is anchored as soon as it enters the dry dock
-
To monitor the ship's stability when the dock's water level is dropped
-
The ship's crew will pump out the ballast once it is positioned on the blocks.
-
This will ready the ship for connecting to shore power.
-
After the dry dock water is pumped out, the crew will use gravity to de-ballast tanks.
-
Take off the drain plugs for each tank from the ship's bottom.
One activity that gives the crew of the ship access to regions they cannot explore while sailing is drydocking.
The ship manager can also use it to evaluate the state of the equipment and the ship's hull, which are inaccessible when the ship is submerged in water.
The crew of the ship and the workers at the dry dock work together to bring the vessel into the dock. The secret to securely placing the ship's keel on the keel blocks is effective communication.

Services Provided:
-
The project's superintendent
-
Visit by a vessel to identify certain docking and fault repair projects.
-
Information gathering from classification societies and other regulatory organizations in order to complete tasks required to meet current or future requirements
-
Creating a comprehensive repair specification
-
Technical Director Anchor's review of the repair specification determining the location of a vessel's docking location, if required, in collaboration with the chartering team and the vessel owners
-
Shipyards are located and contacted to inquire about interest and availability.
-
Repair specification sent out for shipbuilding quotes
-
Shipbuilding bids that are received and assessed similarly
-
Owners receive a finance request and a recommendation for the yard.
-
Subcontractors are appointed and spare parts are ordered.
-
Shipbuilding contract signed
-
Ship finishes dry docking; daily reports are released
-
Every invoice has been received and settled.
-
Report on dry docking issued as needed​
​​
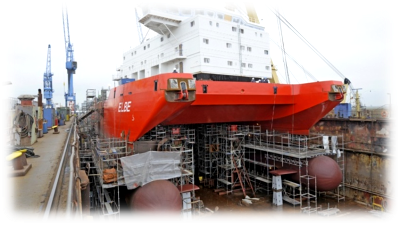
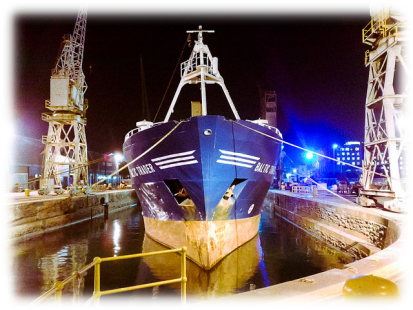